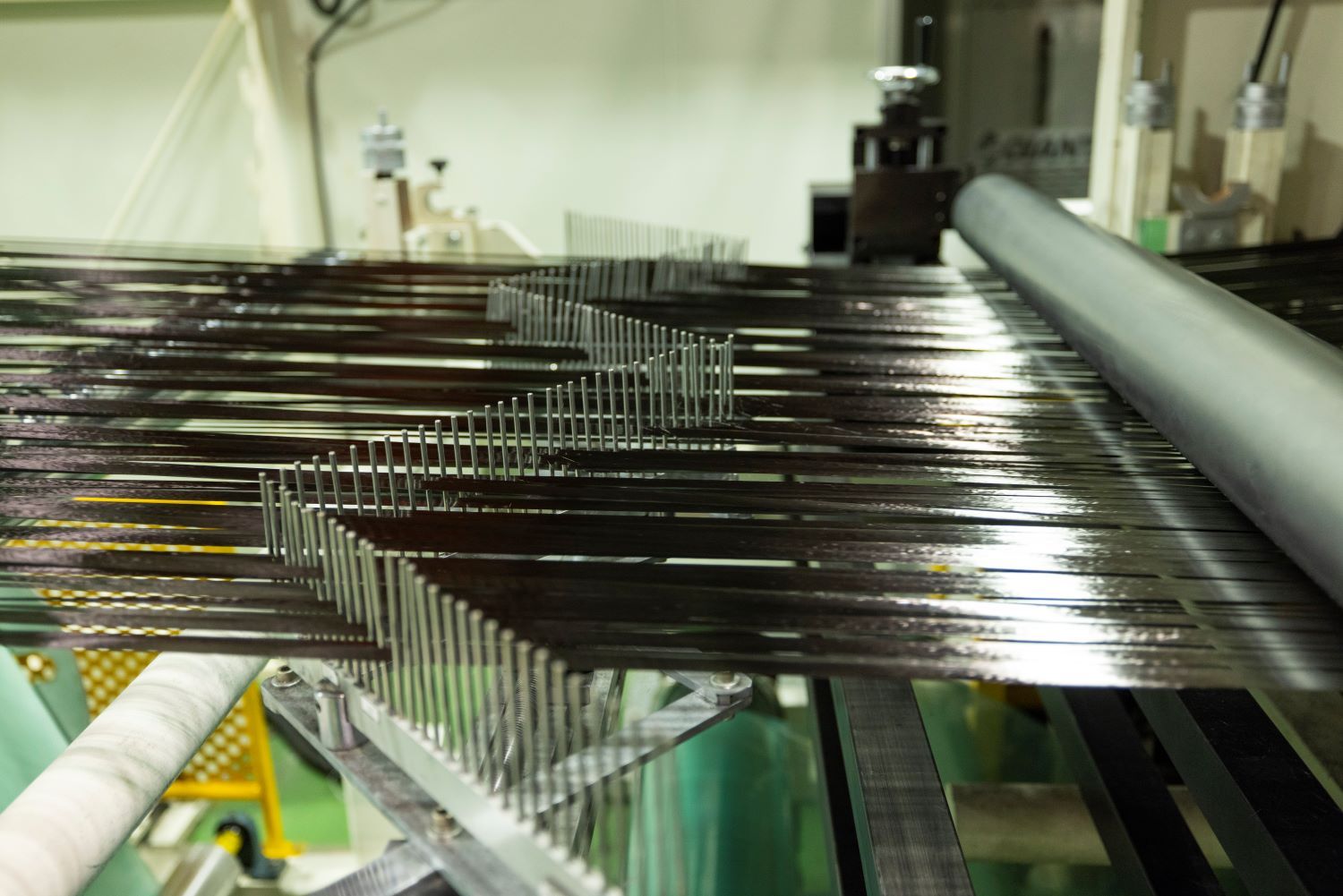
On a visit to Taiwan to be among the first to test the new Giant TCR, Cyclist was also lucky enough to visit the factory where all their top-level carbon products are made – a behind-the-scenes glimpse that provided a new frame of reference for the brand’s craftsmanship
Words Nick Squillari Photography Sterling Lorence
If you’ve spent any time immersed in the world of bikes, you’ve likely encountered the dismissive line: ‘but they’re made by Giant.’ Fifteen years deep into this passion, I’ve heard (and read) it too often.
It’s never said with admiration, always as a slight, whether about a Giant or a bike they presume is made by Giant.
Ask a Giant owner what they love about their bike, and they’ll likely rave about the ride quality or the weight or the value.
Venture into the realm of European bike enthusiasts, and they’ll serenade you with praises of the carbon layup.
The quality of hand-made construction. The workmanship. It’s like a relentless vuvuzela, impossible to ignore.
The illusory truth persists to today: anything crafted in the West is synonymous with bespoke excellence, while products from Asia, especially those from Giant, are relegated to the realm of budget and mediocrity.
If you’ve somehow dodged these debates or avoided the contentious corners of online forums, count yourself fortunate. In many respects this article isn’t aimed at you.
No, I’m speaking to those who harbour doubts about the quality of bikes from Asia.
After a profound journey through Giant’s manufacturing facility, I emerged enlightened, with a newfound appreciation for the excellence they produce.
It’s knowledge that could revolutionise perceptions within the cycling community, challenging long-held assumptions and shedding light on a truth too often overlooked.
Giant Taiwan made the bold decision to coincide the launch of its 10th generation TCR with a factory tour, and it’s anything but ordinary.
Typically, such launches don’t happen in Taiwan.
But Giant wanted to open its doors to the global cycling community, showcasing not just its bikes, but also the stunning scenery the country has to offer.
This wasn’t about frivolity; it was about sharing a passion for cycling, the craftsmanship of bikes, and letting the world know how sensational Taiwan really is for cyclists.
As we toured the factory, it became evident that there’s something truly special about witnessing these processes first-hand.
No online media pack or virtual tour could capture the depth and intricacy of what we saw and experienced.
From the new manufacturing techniques that have been added since the last opening to the media to some of the more candid moments – like spotting other brands that Giant manufacture for (more on that later) – this was about inviting the world to see first-hand the heart and soul of what Giant feels is cycling excellence.
From the very ground up
To my delight, when I arrive at the facility there is actually a giant Giant sign, for what is a rather giant factory complex.
We were told it would take two days for us to walk all of it; there was even a Sram-specific components truck that trundled on past us, such is the size that an internal logistics solution is required. It’s all, well, giant.
Until this point, I had no idea that Giant makes its own prepreg (carbon fibre pre-impregnated with a specific resin mix) carbon sheets.
Starting with Japanese Toray carbon threads, Giant constructs all its Advanced SL models from the very base material up. If that last sentence doesn’t sound like a revelation, it should.
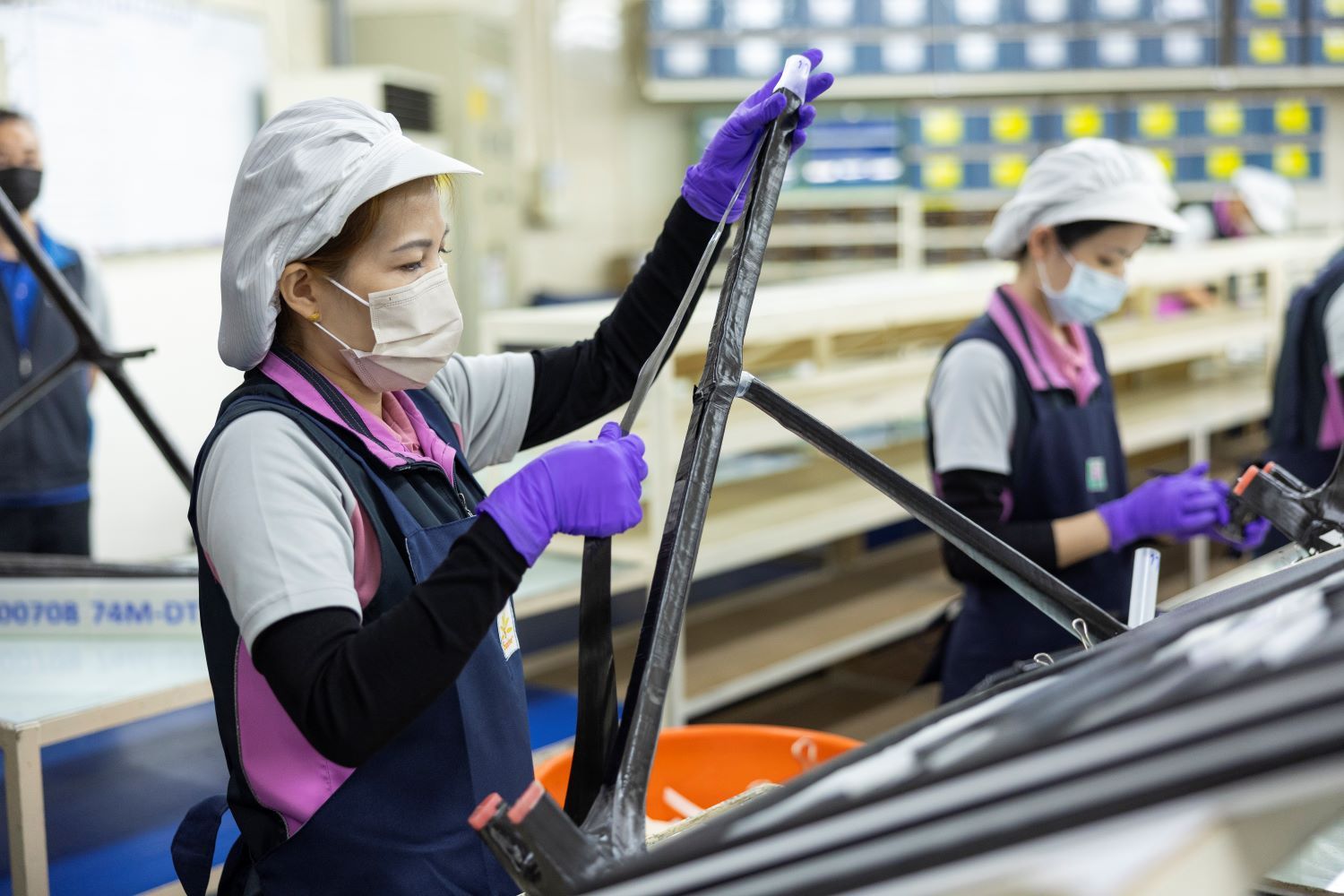
Most brands buy carbon already in prepreg form.
But Giant, by fabricating its own prepreg, gains unprecedented control over the characteristics (weight, stiffness, ride quality) of its frames.
Dozens of spools feed in, unidirectionally, to create the prepreg.
When it comes out it looks a little like a sheet of book contact.
Nondescript to the point where you would walk past and not know what it is – although you would have to be strolling past while the rolls sit in their industrial freezer, which holds anywhere from a 15- to 30-day supply.
Given the number of bikes that go out daily (over 2,700), that’s a lot of carbon.
Fabricating its own prepreg allows Giant to construct composite sheets according to its very own ‘recipe’.
And with over 40 years of knowledge and work with composites, Giant has industry-leading knowledge around honing and refining carbon production.
Interestingly, when asked if they fabricate prepreg for other brands they for whom they make bikes the answer was, ‘Yes – to their specifications.
And even if we disagree on their recipe.’ Poignant. Giant is so exacting and professional that it’ll make your bike precisely how they are specified, even if it’s against their better judgement.
Cold cut and lay-up
While it sounds more like a Michael Jordan drive to the basket, these are actually the next steps in frame fabrication.
Most notable is the cold blade cutting, Giant’s latest advancement for cutting the composite sheets.
Not only does it remove the risk of heat damage that comes with traditional laser cutting, but it’s also more accurate.
This leaves layup pieces cut with greater precision, and with less waste.
Although a few glimpses of this, ahem, ‘cutting-edge’ process have surfaced on YouTube, Giant has otherwise kept a fair element of secrecy around this advancement, such is its ground breaking nature.
The laying up of carbon in the frame fabrication is a process trusted to only the best.
Frame fabricators must first prove their skills in other carbon layup products (like wheels) before they are considered for a role in frame fabrication.
I cannot speak for the je ne sais quoi that one experiences witnessing a traditional ‘bespoke’ carbon frame builder in action, but can vouch it’s impossible not to be captivated by the sheer dedication and expertise on display here.
Each meticulous gesture, each calculated placement of carbon fibre on the single piece mould, bespeaks an unwavering commitment to excellence.
Getting the band together
After curing, facing and finishing, bikes are ready for paint and assembly.
But not before each and every fork is x-rayed.
Whether it’s branded Giant or otherwise, Giant wants us all to keep our teeth. And it’s not just forks; every carbon rim is also sent through the x-ray and assessed.

The room runs 24/7 to keep up with demand. Reassuring.
As is the fatigue testing, where frames are tested to 20% above ISO safety standards at four stages: engineering testing, development testing, pre-production testing and mass production testing.
We witnessed frames being contorted at all kinds of angles. It’s a confidence-inspiring room.
Painting is also done in-house, a process where Giant’s proficiency is on the rise (as evidenced by the TCR’s ‘Maraya Blue’ team frameset as well as the very cool Opal colourway).
Once dry, they roll into assembly where Giant has the process so dialled it only takes 15 minutes. Total. From bare frame to a (basically) rideable bike in less time than it takes me to make breakfast.
Every hour roughly 114 complete bikes are boxed up and ready to go. Watching the efficiency was honestly a thing of beauty.
Emerging from the assembly area, we snatched a tantalising glimpse of frames bearing the insignias of other major brands.
Yet, there was no concealment.
While Giant didn’t provide us an exhaustive list of whom they manufacture for, they also didn’t blindfold us.
The manufacturing landscape has shifted; the balance now tilts decisively in favour of Giant.
Some 70% of bike production is now done by Giant, a production distribution shift now higher than what it was a decade or even five years ago.
Two takeaways jumped out to me on this. First, the Giant brand is going from strength to strength.
Secondly, given the production methods now being deployed, the 30% of Taiwan manufacturing for other brands could only be for high-level frames.
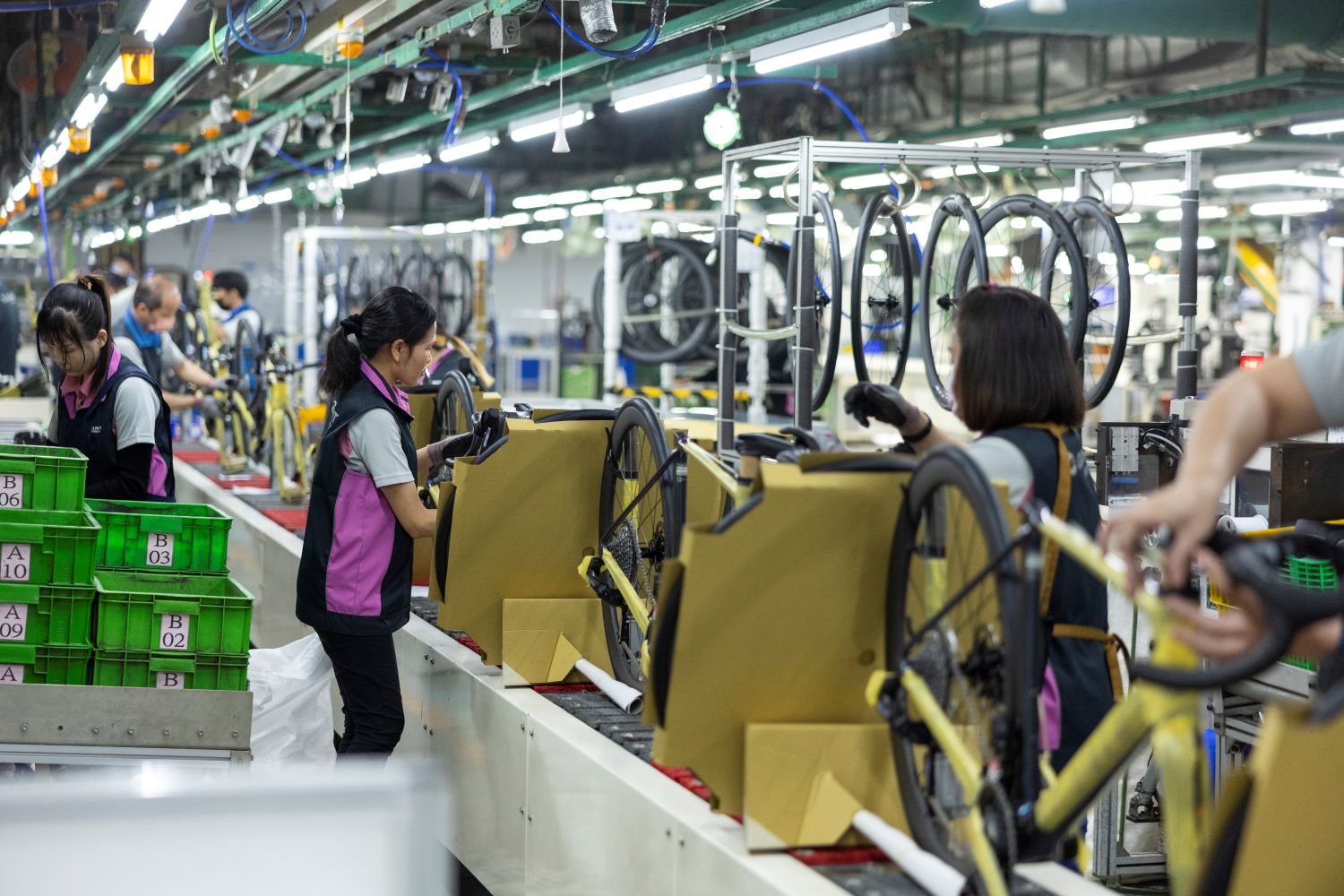
Giant Taiwan is the only factory (of the nine worldwide) that produces the Advanced SL models, so cutting-edge is the tech employed.
There’s simply no way the production process could be down specced efficiently enough to create low spec ‘competitor’ brand frames. The quality, from the Toray threads up, coming out of this facility is exceptional.
I truly believe it’s time the phrase ‘but it was made by Giant’ was punctuated with an exclamation mark.
Whether it’s a Giant frame – or one made by them – it’s clear they are masters of the art in composites. And I for one feel the time for credit is due.
The evolution of Giant’s TCR
1997 The first generation TCR makes its debut, available in three frames sizes with an angle-adjustable quill stem available in three different lengths.
1998 Spanish team ONCE debuts the new TCR at the Tour de France.
2002 The second generation TCR makes its debut at the Tour de France and is the first to feature a full-composite frameset.
2003 The first commercial TCR Composite bikes are available.
2004 The third generation TCR debuts at the Tour de France with the T-Mobile squad. T-Mobile goes on to win the team classification for the next three years (2004-06).
2005 The fourth generation TCR is introduced with an integrated seatpost.
2008 The fifth generation TCR is introduced with several new technologies including a press-fit bottom bracket and integrated cable routing. Mark Cavendish (Team Columbia Highroad) wins four stages on a TCR Advanced SL.
2009 Denis Menchov (Team Rabobank) wins the Giro d’Italia on a TCR Advanced SL.
2012 The sixth generation TCR debuts at the Tour de France with Team Rabobank.
2015 The seventh generation TCR debuts at the Tour de France with Team Giant-Alpecin.
2016 The eight-generation TCR, with integrated disc brakes, is introduced.
2017 Tom Dumoulin (Team Sunweb) wins the Giro d’Italia on a TCR.
2020 The ninth generation TCR is introduced.
2022 Simon Yates (Team Jayco AlUla) rides the TCR Advanced SL to victory in stages of both Paris-Nice and the Giro d’Italia.
2024 The 10th generation TCR is unveiled in Taiwan – and Cyclist gets a behind-the-scenes glimpse on a visit to the GTM factory.